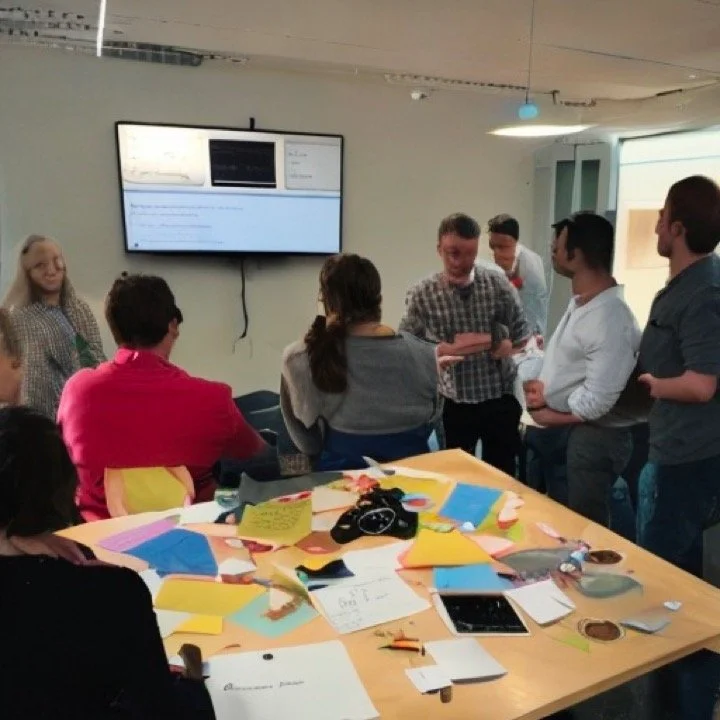
The range of Human Factors topics includes:
-
Alarm Systems
Alarm systems are an essential part of the SCADA control room system; they are required to alert the operator to a range of situations and system state changes. Alarm systems are necessary given the sheer amount of information contained within the control systems. In a typical SCADA system, operators can be monitoring up to 800 pages of information and up to 20,000 alarms. The design of the alarm system has a significant effect on the performance of the operator. A well-designed alarm system considers the operators ability to; recognise the situation, diagnose the fault, and develop a suitable course of action.
-
Automation
Automation addresses the dichotomy of scheduling tasks between humans and machines. An automated device is, by definition, able to operate without human input, but automation does tend only to work effectively within prescribed system limits. Often this relegates the human role to one of monitoring the automated systems, only intervening if they fail to cope. Allocation of function methods have been developed to assist in the appropriate design of automation. A socio-technical approach is advocated, which employs automation (i.e., the technical part of the system) in a manner that designs meaningful work for people (i.e., the social part of the system).
-
Communications
Communication refers to ‘information exchanged’ and/or the presence of a ‘connection’. This refers to communication between people in any medium available (e.g., via voice, telephone, notes, messages, email, msn, etc.) as well as communication between people and technology (e.g., via information displays and controls). Poor communications in control rooms can result in: Missing information, unnecessary information, inaccurate information, poor or variable quality of information, misunderstandings, failing to carry forward information over successive shifts. Ineffective information exchange and/or the lack of an appropriate ‘connection’ have led to a number of major incidents.
-
Competencies
The safe and efficient working environments are dependent upon the competence of the people working within them. Further, the design of work should be based on a thorough understanding of human abilities and constraints. The term competency is generally used to describe individual attributes associated with the quality of work performance, but can also refer to a team’s job-related attributes and also to an overall organisation’s attributes. The identification, training, maintenance, monitoring and assessment of competencies is critical for ensuring that staff possess the appropriate competence levels required for safe and efficient work performance.
-
Control Room Layout
Control Room Layout refers to the functional and physical structure of the room and associated workstations (including desks, chairs, computers, peripherals and storage cabinets) where operators are stationed to conduct centralised monitoring and control activities. Control Room Layout is a significant factor in efficient system control. The work of the control room staff can be extremely demanding, so well-designed rooms and workstations can increase the physical comfort operator as well as reduce stress levels and increase efficiency. Human Factors methods , such as link analysis and layout analysis, are particularly useful in desiging the layout of control rooms.
-
Human-Machine Interface
Human-machine interaction refers to the dynamic relationship and interaction between humans and machines, particularly in the context of technology and computing systems. It encompasses the ways in which humans interface, communicate, and collaborate with machines, such as computers, robots, or other automated systems. Human-machine interaction involves the design, development, and evaluation of interfaces and interactions that facilitate effective and intuitive communication between humans and machines. It seeks to create interfaces that are user-friendly, efficient, and enable seamless information exchange and task execution. The goal is to enhance productivity, usability, safety, and user satisfaction while optimising the collaboration and cooperation between humans and machines in various domains.
-
Human Error
Human error covers the many types (slips, lapses and mistakes), causes (both in the workplace and the work system) and consequences of failure by personal to completed tasks successfully. It is assumed that human error is an inevitable consequence of normal performance and therefore the system needs to be as error tolerant as practically possible. Also, that blaming individuals for errors does not make systems safer. Typically, the focus of human error is on so-called ‘sharp-end’ factors; those factors that are close to the error events in time and space. Consideration should also be given the so-called ‘blunt-end’ factors; those factors that create the conditions which make the errors more likely (sometimes called latent conditions).
-
Incident Investigation
Incident investigation is the formal process of finding out what happened and why it happened with the aim of preventing reoccurrence of similar events in the future. Many different methods are used in incident investigation, normally starting with a timeline of actors and events. Investigations are normally based on witness statements, data from equipment, photographs of the equipment, and relevant documents, such as procedures, equipment specifications, and permits. Investigations aim to identify the likely multiple root causes (both at the sharp-end and at the blunt-end of systems) so that preventative measures can be developed, including changes in equipment and procedures, additional responsibility and lines of reporting, identification of new competencies, and new training requirements.
-
Maintenance, Inspection and Testing
Maintenance, inspection, and testing are integral components of ensuring the reliability, performance, and safety of equipment, systems, and infrastructure. Maintenance involves planned activities aimed at preserving, repairing, or upgrading assets to keep them in optimal condition and prevent failures or breakdowns. Inspection is the process of visually or systematically examining components or systems to identify any potential defects, wear, or non-compliance with standards or regulations. Testing involves conducting controlled experiments or assessments to validate the functionality, performance, or compliance of equipment or systems. By combining these practices, organizations can proactively identify and address issues, extend the lifespan of assets, minimize downtime, and maintain operational efficiency while promoting safety and compliance.
-
Procedures
Operating procedures provide a description of the actions or steps required in order to perform a task safely and efficiently. The provision of appropriate, efficient procedures is essential for safe and efficient operator performance in the safety critical domains, particularly when faced with non-routine or emergency situations. Problems associated with operating procedures, such as inappropriate or incorrect procedures or lack of procedures have been implicated in a number of high-profile catastrophic accidents and incidents, including the Bhopal, Piper Alpha and Clapham junction disasters. There are a number of key issues surrounding the application of procedures, including issues related to their development and maintenance, their efficacy and usability as well as workers compliance with them.
-
Safety Culture
Safety culture refers to the collective values, attitudes, beliefs, and behaviours within an organisation that prioritise and promote the well-being of individuals and the prevention of accidents and injuries. It is characterised by a strong commitment to safety at all levels, from leadership to frontline workers, and encompasses open communication, trust, and accountability. A positive safety culture fosters a proactive approach to identifying and mitigating risks, encourages employee engagement in safety practices, and supports continuous improvement. It emphasises the integration of safety into daily operations, empowering individuals to take responsibility for their own safety and the safety of others.
-
SCADA
The design of the Supervisory Control and Data Acquisition (SCADA) system is integral to the performance of the system, in terms of safety, efficiency and effectiveness. SCADA systems have essentially two main roles, communicating information from physical sensors within the plant and facilitating physical manipulations to component with the system. Descriptions of the controlled system can be presented at a number of levels of abstraction. Theses descriptions range from physical raw data from individual sensors, up to higher order systems performance descriptions calculated through data fusion. Early SCADA systems were comprised of a series of readouts, directly hard-wired to the physical objects they represented. These hard-wired display consoles were generally, large, fixed and difficult to modify. The advent of the microchip has allowed many of these systems to be digitised. It is now possible to remotely control these systems with mechanisation, computers and appropriate software.
-
Shiftwork
Shift patterns refer to the scheduling of work activity outside the standard office hours, such as in 24/7 operations in control rooms. These operations assume continuous staffing and a handover of duty from one team to another. Shift work quite often brings compensation in terms of better pay, time off, flexible working and so on, there are also numerous issues and risks for the individual as well as the system as a whole that require careful consideration. Individual risks and issues have been grouped into the following four headings: sleep and the biological clock, social challenges (especially for families), stress and strain and health consequences. Whilst shift work is commonly associated with individuals who have to work during the night, working at other times can be equally, if not more, disruptive to the individual concerned and ultimately to the performance of the system they are working within.
-
Staffing and Workload
Staffing refers to the the number of people working together at any one time. The level of staffing is of critical importance to performance and overall system safety. In recent times an increase in the levels of automation, team working and multi-skilling has led to a general reduction in the staffing levels used and there are concerns that this could adversely impact system performance and safety through increases in workload and its associated consequences. Ideally, staffing levels should be sufficient for both normal and abnormal situations. Inappropriate workload levels (both too high and too low) have a range of adverse consequences, including fatigue, errors, monotony, mental saturation, reduced vigilance and stress.
-
Supervision
Supervision involves controlling, influencing and leading a team and includes activities such as directing the work of others, allocating tasks and workload, planning and scheduling of tasks. Supervisory activities imply authority, responsibility and accountability (such as maintaining team discipline), but they also imply fostering team spirit and developing the capability of team members. In 24/7 control room teams, supervisory arrangements typically have three main facets. Within normal office hours supervisory arrangements typically have the traditional formal hierarchical line management structure. Within the control room there is also a coaching and mentoring. Outside the normal office hours there is also the additional self-managed team aspect to the 24/7 control room operation.
-
Training
Training is a critical factor in safe and efficient organisational performance. A skilled and prepared workforce can yield higher productivity and better service, improved quality, higher motivation and commitment, fewer errors, increased safety, together with greater levels of teamwork and morale. Training is formally defined as the systematic acquisition of knowledge (i.e. what we need to know), skills (i.e. what we need to do), and attitudes (i.e. what we need to feel) that together lead to improved performance in a particular environment. On a simpler level training is about people getting the right competencies to do a job. Organisations wishing to deliver successful training programs therefore need to carefully consider all aspects of training program design, delivery and evaluation. A summary of the key issues involved is presented below.
-
Working Environment
The working environment refers to the prevailing ambient conditions, such as temperature, air quality, lighting, acoustics, vibration, interior design and aesthetics, that are likely to have an effect on human performance, particularly in 24/7 operations. Environmental agents (and their effects) do not occur in isolation. The subjectively felt state often arises as a ‘product’ of individual environmental agents rather than their mere summation. A good deal of effort involved in creating an optimum working environment is in managing trade-offs between apparently conflicting goals. For example, an optimum temperature may only be achievable with an increase in noise from ventilation equipment. Likewise, the corollary of sound emission is vibration, the physical attenuation of one can exacerbate the other. Adopting a systems perspective, and in doing so recognising the interrelatedness of environmental factors
-
Workstation Design
Workstation design refers to the ergonomic arrangement of physical elements and equipment within a workspace to optimise the comfort, safety, and productivity of the individuals using it. It encompasses factors such as the layout, furniture, lighting, ventilation, noise control, and accessibility. A well-designed workstation takes into account human factors, such as body posture, reach, visibility, and task requirements, to minimize the risk of musculoskeletal disorders and fatigue. It promotes proper alignment, adjustability, and support for the body, as well as efficient organization of tools and resources. Effective workstation design contributes to a healthy and conducive work environment, enhancing employee well-being and performance.
Contact me
If you want a world-leading Human Factors expert to help you, then please fill out the form and send it to me: